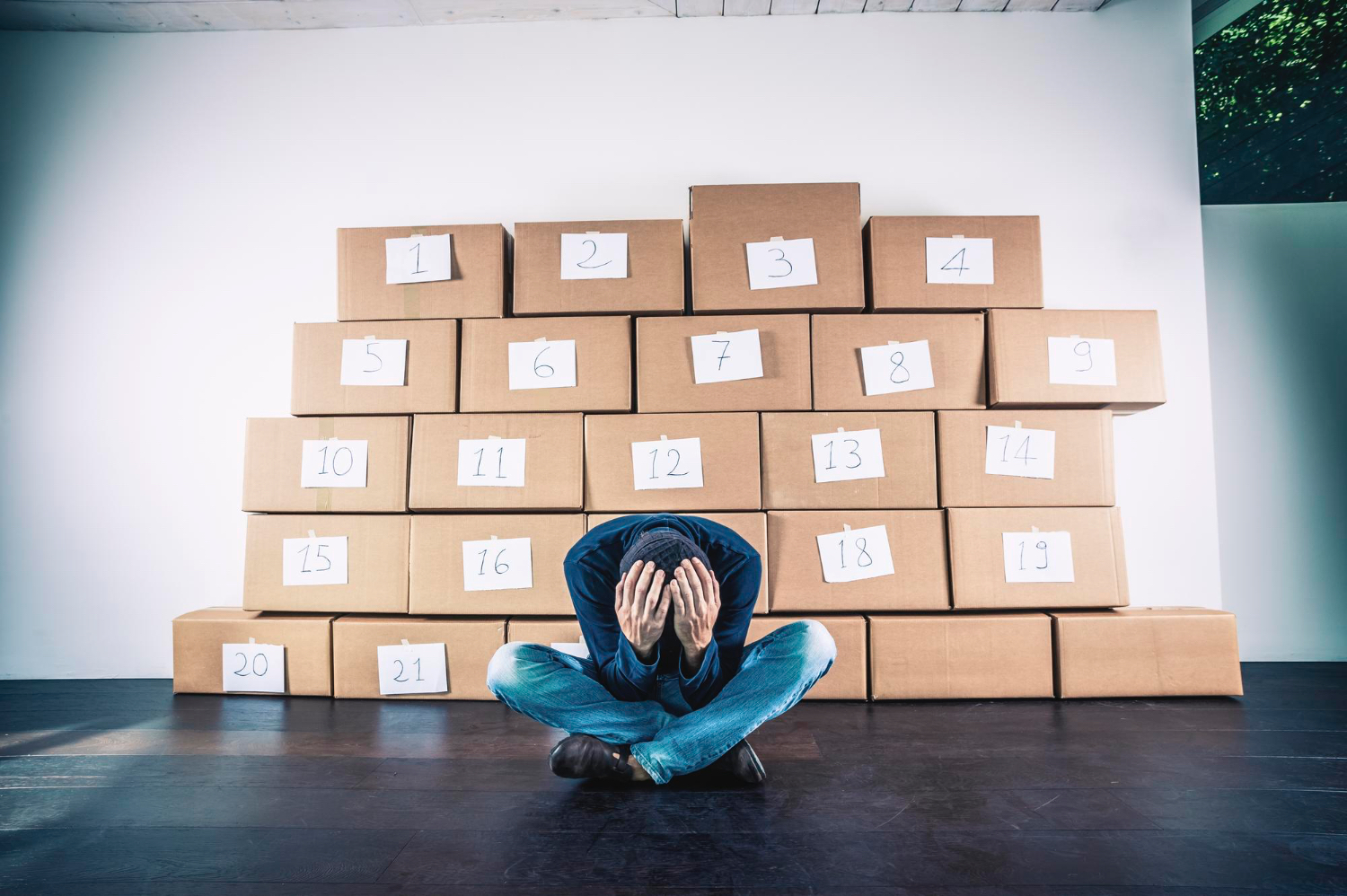
Enterprise Resource Planning (ERP) systems can’t see Operations!
Some time ago a plant manager friend of mine told me he always felt like he was “flying blind” with his ERP system. “It tells me the jobs that are started and finished, but Operations happen in the middle, and I have no visibility on how my assets are being consumed until it’s all over, and then it’s too late to make any difference.”
I could understand his unease, but the true risk of this, “ERP Doughnut” was brought home to me recently when I heard of a real train-wreck at an unrelated plant.
In a nutshell, an audit showed up some serious inventory shortfalls which required painful balance-sheet write-downs. An investigation revealed that Work Orders weren’t getting closed when the jobs were completed so all the stocks were out of whack.
The Purchasing Department kept buying at regular volumes because they knew from experience the parts would be needed. The Accounts Department could see Work-In-Progress values going up, but in Operations there was the same amount of physical goods around the place so everything looked fine.
I thought of my friend worrying that he was “flying blind”, and realised that notwithstanding management failures, their ERP system gave them little indication that anything was wrong.
Wouldn’t it be nice if there was a system that had your back. One with Operational Analytics that could work in this blind-spot, make sense of what it was looking at, and Predict what the outcome was going to be while there was still time to do something about it? One that wouldn’t just keep you out of trouble, but constantly make better and better predictions, as it learned more about your operations?